Chemical lobe pump is a type of pump commonly used in the chemical industry. Its structure is usually similar to that of a general rotor pump. It is mainly used to transport various chemical liquids, slurries, pastes, etc. The materials of the flow-passing parts of chemical rotary pumps are usually made of materials with good corrosion resistance and wear resistance to adapt to the special process requirements in the chemical industry. Its main configuration usually includes the following parts:
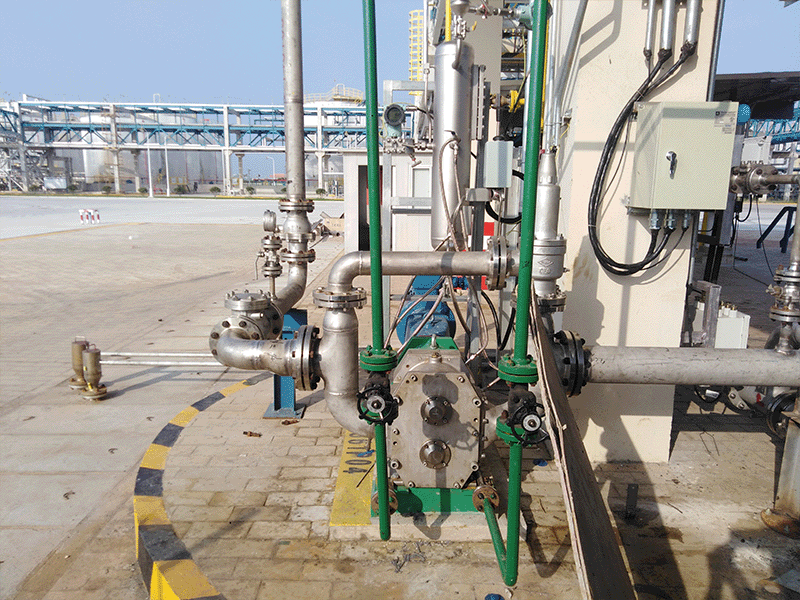
- 1. Pump body (casing): The pump body is the main load-bearing component of the pump. It is usually a stationary shell whose interior matches the shape of the rotor to form a sealed working chamber. The geometry and structure within the housing determine the movement path of the liquid when the rotor rotates. It is usually made of corrosion-resistant metal (such as stainless steel) or special alloy materials to withstand pressure and resist corrosion.
- 2. Lobe (rotor): The design of the lobe (rotor) is the core of this type of pump. It is usually two spiral rotating parts that produce the suction and discharge effects of the pump through rotational motion. The shape and material of the lobe (rotor) will vary according to the user's media conditions. The lobe (rotor) is located in the pump casing and is a rotating component within the pump. It is usually made of metal and non-metallic materials. Its shape and number will affect Pump performance parameters, such as flow, head, etc.
- 3. Seals: Chemical lobe pumps need to consider sealing performance to prevent liquid leakage, so they are usually equipped with seals, such as mechanical seals.
- 4. Driving device: Provides the power required for pump operation, usually an electric motor. Its selection will take into account the power requirements and working environment of the pump.
- 5. Inlet and outlet flanges: Inlet and outlet flanges used to connect pumps and piping systems. They usually have standard sizes and connection methods to facilitate installation and disassembly.
- 6. Base: The basic structure that supports the pump and its related components, usually made of steel to provide stable support and installation.
- 7. Control device: If necessary, the Chemical lobe pump may also be equipped with a control device to monitor and adjust the operating status of the pump, such as flow, pressure and other parameters.
These are the main configurations of Chemical lobe pumps. Pumps of different models and uses may differ. The specific configurations will be selected and designed according to actual needs and process conditions.
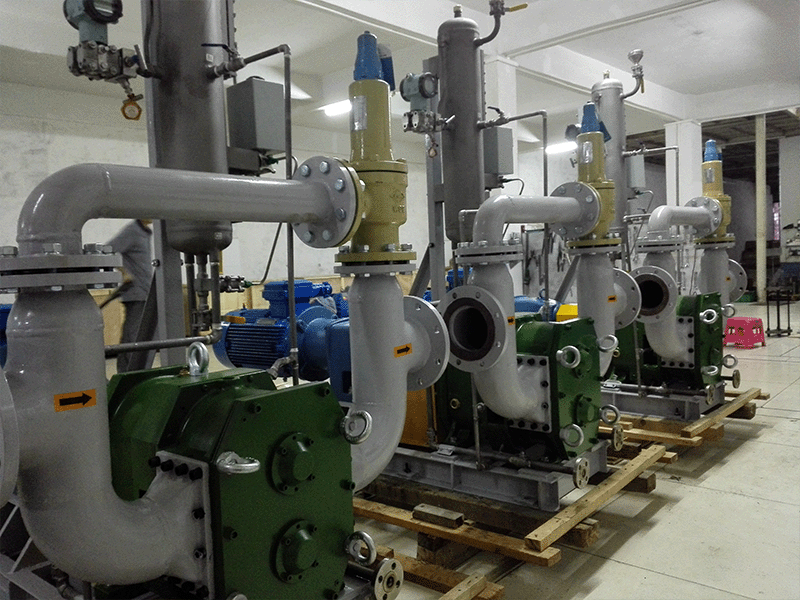
- 1. Strong adaptability: Chemical lobe pumps can adapt to various chemical media, including corrosive liquids, high-viscosity liquids, high-temperature liquids, etc., and perform stably and reliably under different working conditions.
- 2. Good stability: The design and working principle of the pump make its operation stable and the flow and pressure fluctuations generated are small, which is conducive to the stability and quality control of the production process.
- 3. High efficiency: Chemical lobe pumps can provide efficient liquid transportation, with high transportation capacity and efficiency, helping to improve production efficiency and reduce energy consumption.
- 4. Energy saving and environmental protection: Some Chemical lobe pumps adopt advanced design and technology to reduce energy consumption and production costs, while also helping to reduce the impact on the environment and comply with environmental protection requirements.
- 5. Low maintenance cost: usually with a simple structure and a small number of wearing parts, the maintenance and repair costs are relatively low, which is beneficial to reducing production and operation costs.
- 6. Flexibility: Chemical lobe pumps can be customized and designed according to different process requirements to meet liquid transportation needs under different working conditions and have high flexibility.
- 7. Strong reliability: After strict quality control and testing, the Chemical lobe pump has high reliability and safety, and can operate stably for a long time, ensuring the continuity and stability of the production process.
To sum up, the Chemical lobe pump has the characteristics and advantages of strong adaptability, good stability, high efficiency, energy saving and environmental protection, low maintenance cost, strong flexibility and reliability, etc., and provides a reliable liquid transportation solution for the chemical industry. Helps improve production efficiency and ensure safe production. Rotor pumps are widely used in chemical production and are often used in liquid mixing, transportation, processing, etc., providing reliable liquid transportation solutions for the chemical industry.
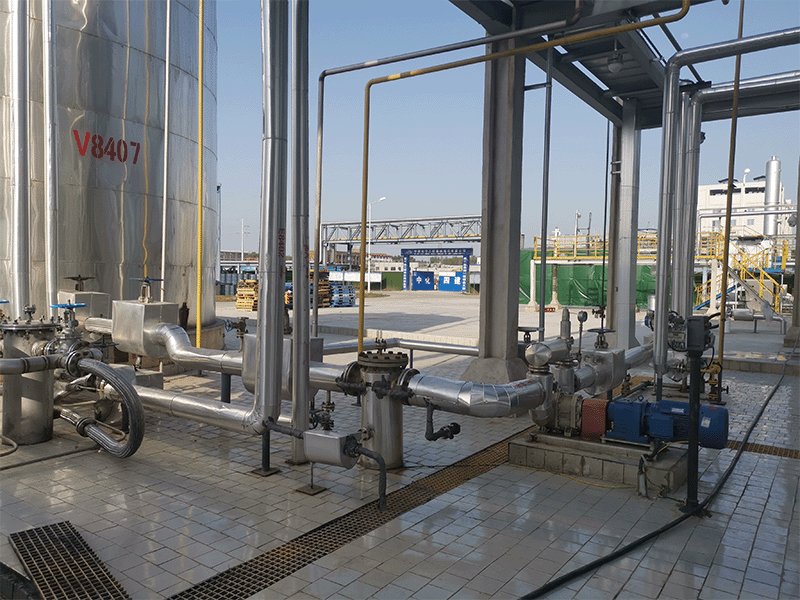
Chemical lobe pumps have a wide range of applications in the chemical industry, mainly including the following aspects:
- 1. Liquid transportation: Chemical lobe pumps are often used to transport various liquids, including solvents, acid and alkali solutions, chemicals, polymers, resins, etc., for raw material transportation, intermediate transportation, and finished product transportation during the production process.
- 2. Reaction process: In the chemical reaction process, Chemical lobe pumps are used to transport reaction materials, intermediates and reaction products to ensure the smooth progress of the reaction process, such as raw material supply and product discharge in chemical reactors.
- 3. Processing technology: Chemical lobe pumps also play an important role in chemical processing technology. They are used for stirring, mixing, dilution, cooling and other process steps to provide necessary liquid transportation support for product processing.
- 4. Wastewater treatment: In wastewater treatment projects, Chemical lobe pumps are used to transport wastewater, sewage, sludge, etc. to treatment facilities for treatment to protect the environment and water resources.
- 5. Environmental protection facilities: Chemical lobe pumps are also used in environmental protection facilities, such as liquid transportation in flue gas desulfurization, flue gas denitrification, waste gas treatment, etc., to help reduce the impact of emissions on the environment.
- 6. Laboratory and R&D: In chemical laboratories and R&D centers, Chemical lobe pumps are used for small-scale testing and research, and are used for sample processing, solvent transportation and other experimental needs.
- 7. Petrochemical industry: In the petrochemical industry, Chemical lobe pumps are used in crude oil processing, refining processes, petroleum product transportation and other links.
To sum up, Chemical lobe pumps are widely used in the chemical industry, covering multiple links in the production process, providing reliable liquid delivery solutions for chemical production.
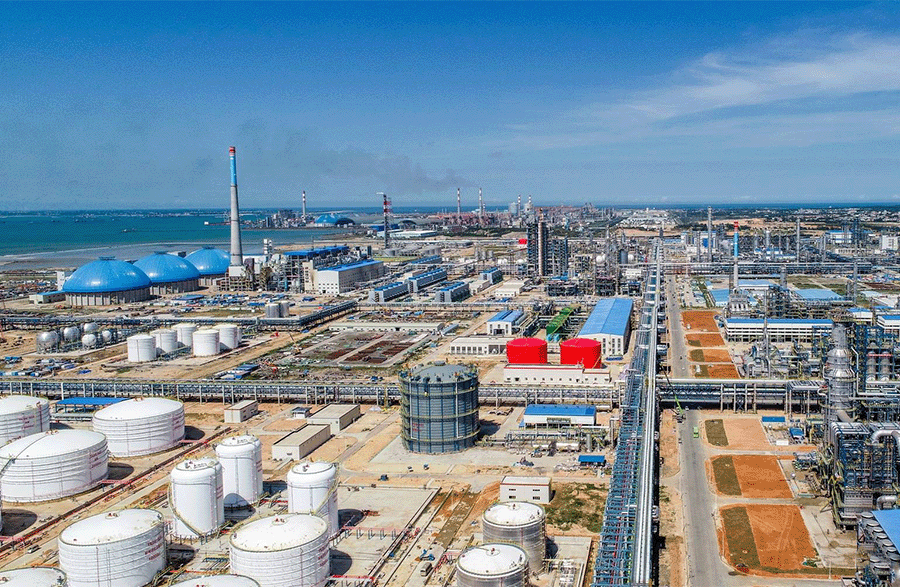
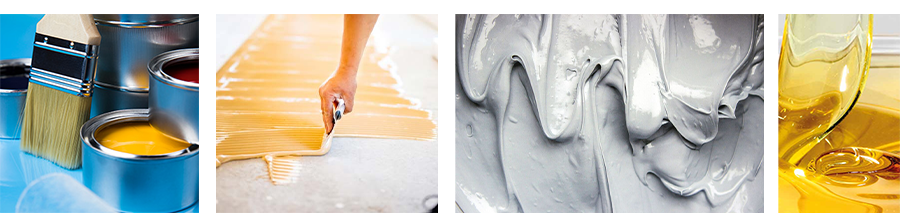